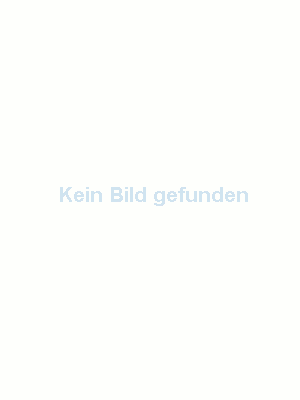
×
Analyse und Entwicklung des Extrusionsprozesses zur Erhöhung der Dispersionsqualität von Nanopartikel-Polyamid 6-Verbundwerkstoffen
von Irene HassingerKurzfassung
Sphärische keramische Nanopartikel können die Eigenschaften von Thermoplasten
signifikant positiv verändern. Eine gute Dispersität von Nanopartikeln in einer polymeren
Matrix ermöglicht z. B. eine außergewöhnliche Steigerung der Zähigkeit. Allerdings
neigen die Nanoadditive wegen ihrer großen spezifischen Oberfläche zur Agglomeration,
was der Verbesserung der Eigenschaften entgegenwirkt. Dies stellt eine der
größten Herausforderungen der Nanokompositforschung dar. Da industriell hergestellte
Nanokomposite von steigendem Interesse für vielerlei Anwendungen sind, ist es
ingenieurwissenschaftlich relevant, Prozess-Struktur-Eigenschaftsbeziehungen von Nanokompositen
mit kommerziell erhältlichen Nanopartikeln genauer zu verstehen. Dies
erlaubt eine gezielte Steuerung bzw. Einstellung der Materialeigenschaften.
In den bisherigen wissenschaftlichen Arbeiten zu thermoplastischen Nanokompositen
mit sphärischen keramischen Nanofüllstoffen ist die Dispersität der Nanokomposite
nicht hinreichend gut quantifiziert worden, was zur Folge hat, dass verschiedene Herstellungsmethoden
nicht miteinander verglichen werden können. Diese Arbeit zielt darauf
ab, thermoplastische Polyamid 6-Nanoverbundwerkstoffe mit guter Dispersität mittels
Extrusion herzustellen und zu untersuchen. Dabei werden drei Herstellungsmethoden
und die dabei erreichten Dispersionsqualitäten und Eigenschaftsprofile betrachtet. Dafür
werden Verbundwerkstoffe aus einer PA6-Matrix und keramischen Nanofüllstoffen (TiO2,
SiO2, BaSO4) - als Pulver oder als Nanopartikeldispersion - generiert. Die erzeugten
Komposite werden mit TEM-, REM- und -CT-Analysen morphologisch analysiert. Die
Materialeigenschaften werden durch DSC-, DMTA-, GPC-, Viskositätsuntersuchungen
erfasst. Weiterhin werden Kerbschlagbiege- und Zugversuche durchgeführt.
In einem ersten Schritt wird eine häufig angewendete Herstellungsmethode untersucht,
bei der Nanopartikelpulver zum Extrusionsprozess zugegeben werden. Es ist
nicht möglich alle Agglomerate durch die Bearbeitung im Extruder aufzubrechen. Die
Agglomeratfestigkeit für die verwendeten Partikel wird aus den Verläufen der Dispersität
bei mehrfacher Extrusion erfolgreich bestimmt. Die Untersuchung der Vorgänge
bei der Deagglomeration anhand eines Modells zeigt, dass das Verhältnis zwischen
Agglomeratbruch und Erosion von einzelnen Partikeln von der Oberfläche des Agglomerates
für die Materialeigenschaften von maßgeblicher Bedeutung ist. Trotz sehr guter
Dispersionsqualität der TiO2-Komposite und einer guten Partikel-Matrix-Anbindung lassen
sich nur die Festigkeit und Steifigkeit steigern, während die Kerbschlagzähigkeit
vi Kurzfassung
nicht erhöht ist. Die TiO2-Nanopartikel weisen eine relativ geringe Agglomeratfestigkeit
(0,1 MPa) auf, und die Erosion spielt neben Bruch eine wichtige Rolle im Deagglomerationsmechanismus,
weshalb für diese Partikel die Zugabe als Pulver zu empfehlen
ist. Restagglomerate führen jedoch zu Spannungskonzentrationen im Material, was
eine Zähigkeitssteigerung verhindert. SiO2-Nanopartikel dagegen können bei den in
dieser Arbeit gewonnenen Erkenntnissen nicht als Füllstoffe empfohlen werden. Ihre
Agglomerate weisen eine so hohe Festigkeit auf, dass diese überwiegend zerbrechen.
BaSO4 sollte als Pulver nicht verwendet werden, denn es kann mittels Extrusion kaum
dispergiert werden.
In der zweiten Bearbeitungsphase werden die Materialeigenschaften bei der Zugabe
der Nanopartikel als wässrige Dispersion untersucht. Dabei wird die Partikeldispersion
drucklos zugegeben; das Dispersionsmedium kann an der Zugabestelle direkt verdampfen.
Zusammengefasst ist festzustellen, dass Agglomeration an der Zugabestelle zu
verschlechterten mechanischen Eigenschaften führt.
Im dritten Schritt werden wässrige Nanopartikeldispersionen unter Druck in den Extruder
gepumpt, um zu erreichen, dass sich eine Mischung aus flüssiger Dispersion und Polymerschmelze
bildet. Dabei tritt zum einen Diffusion der Partikel in die Polymerschmelze
auf, zum anderen kommt es zu Tropfenverkleinerung durch die Scherspannung im
Extruder. Bei der theoretischen Untersuchung der Zerkleinerung der Dispersionstropfen
wird festgestellt, dass das Verhältnis der Viskositäten der zu mischenden Medien, deren
Oberflächenspannungen und die Scherspannung im Extruder den Vorgang bestimmen.
Die so ermittelte Größe der kleinsten Agglomerate liegt nicht im Nanometerbereich.
Infolge der geringen Mischdauer nach der Verdunstung des Dispergiermediums sind die
Agglomerate schlecht an die Matrix angebunden. Weiterhin bilden sich sehr kompakte
Agglomerate. Aufgrund dessen steigert sich der E-Modul des Nanokomposits kaum
bei einer gleichzeitig reduzierten Zähigkeit. Als Dispersion zugegeben diffundieren die
SiO2-Partikel kaum und es bilden sich relativ große Agglomerate. Da insbesondere bei
TiO2 und BaSO4 außergewöhnlich kleine Agglomerate (<100 nm) bzw. sogar Primärpartikel
gefunden werden, ist davon auszugehen, dass für diese beiden Nanoadditive
auch Diffusion von Bedeutung ist. Nanokomposite mit diesen Füllstoffen sollten über
die Methode der Zugabe von wässrigen Dispersionen unter Druck hergestellt werden.
Diese Arbeit bildet mit systematischen Untersuchungen von industriell relevanten Prozessen
zur Herstellung von Nanokompositen, den Mechanismen, die dabei ablaufen,
und den erzielbaren Materialmorphologien und Materialeigenschaften die Grundlage
für maßgeschneiderte Nanokomposite.
vii
Abstract
Ceramic spherical nanoparticles can significantly increase the properties of thermoplastic
polymers. Well-dispersed nanoparticles can exceptionally increase the material
toughness of polymers. However, agglomeration, which occurs because of an extremely
large specific surface area of the particles, can counteract this behavior. This
is one of the major challenges in nanocomposite science. As industrially produced
nanocomposites are of increasing interest for all kinds of applications, the research of
process-structure-property-relationships of nanocomposites with commercially available
nanoparticles is crucial in engineering science. This allows the control of the material
properties.
Most existing publications about thermoplastic nanocomposites with ceramic spherical
nanofillers do not quantify the dispersity of the products sufficiently. Consequently, the
different production methods cannot be compared. This work studies thermoplastic
polyamide 6 nanocomposites that were produced by extrusion processing in order to
achieve a good dispersion quality. To complete this task, three production methods were
applied and the resulting dispersion quality was analyzed. For this, nanocomposites
consisting of a PA6 matrix and TiO2-, SiO2- and BaSO4-nanofillers - as powders or as
dispersions - were produced. Structural analysis was performed by electron microscopy
and computer tomography. DSC, DMTA, GPC, and viscosity measurements were
executed, and impact and tensile tests conducted.
In a first step, the traditional production method of thermoplastic nanocomposites, where
nanoparticle powders are incorporated in the polymer melt, was analyzed. It was found
that it was impossible to reduce all agglomerates by extrusion. The agglomerate strength
was successfully determined from the dispersion quality when multiple extrusion was
applied. Furthermore, a model revealed the appearing mechanisms of erosion of single
nanoparticles from the agglomerate surface and agglomerate breakage. It was found
that breakage was the dominant mechanism of deagglomeration. Despite very good
dispersion quality of the TiO2-composites and a strong particle matrix interaction, only
material stiffness and strength could be increased, while the impact energy was not
increased. TiO2-nanoparticles are favourable for powdery addition, due to their relatively
small agglomerate strength (0,1 MPa) and the important part that erosion also played in
the deagglomeration mechanisms. Remaining agglomerates behaved as large single
particles and acted as initiation sites for brittle crack behavior. SiO2-nanoparticles are
viii Abstract
not recommended as powdery fillers, because they built very strong agglomerates, that
only exhibit breakage as deagglomeration mechanism. BaSO4 is not recommended as
filler in powder form because of the lack of deagglomeration.
In a second step, the material properties were examined, when the nanocomposites
were produced by unpressurized insertion of aqueous nanoparticle dispersions into the
polymer melt. The dispersion media evaporated immediately after insertion. However,
agglomerates generated during extrusion resulted in reduced mechanical properties.
In a third step, aqueous nanoparticle dispersions were incorporated using enough
pressure to build a blend consisting of dispersion and polymer melt. Two mechanisms
occurred during this process. On the one hand, particles diffused from the dispersing
agent into the polymer melt. On the other hand, bigger drops of the aqueous nanoparticle
dispersion were reduced to smaller ones by shear stresses during extrusion. The
smallest drop size occurring in the latter process could be determined. This size was
affected by the ratio of the viscosity of the media, their surface tensions and the shear
stresses in the extruder. The such calculated smallest agglomerate size was not smaller
than 100 nm in the pursued range. As a result of the short mixing duration after
evaporation of the dispersion fluid, agglomerates were poorly bonded to the matrix.
Furthermore, very dense agglomerates were formed. Thus, the toughness was reduced
while the Young’s modulus could hardly be increased. As dispersions, SiO2-particles
did not undergo a diffusion mechanism ending up in big remaining agglomerates. As
remarkably small nanoparticle agglomerates (<100 nm for TiO2) and primary particles
(BaSO4) could be found, it could be assumed that the diffusion mechanism also occurred.
Thus, the pressurized insertion of nanoparticle dispersions represents an adequate
production method for nanocomposites with BaSO4 and TiO2 as fillers.
This work can be considered as a systematic research on production methods for nanocomposites,
the mechanisms playing a part and the material structures and properties
that are gained. Within the new results and findings of this work it is possible to tailor
nanocomposites.
Sphärische keramische Nanopartikel können die Eigenschaften von Thermoplasten
signifikant positiv verändern. Eine gute Dispersität von Nanopartikeln in einer polymeren
Matrix ermöglicht z. B. eine außergewöhnliche Steigerung der Zähigkeit. Allerdings
neigen die Nanoadditive wegen ihrer großen spezifischen Oberfläche zur Agglomeration,
was der Verbesserung der Eigenschaften entgegenwirkt. Dies stellt eine der
größten Herausforderungen der Nanokompositforschung dar. Da industriell hergestellte
Nanokomposite von steigendem Interesse für vielerlei Anwendungen sind, ist es
ingenieurwissenschaftlich relevant, Prozess-Struktur-Eigenschaftsbeziehungen von Nanokompositen
mit kommerziell erhältlichen Nanopartikeln genauer zu verstehen. Dies
erlaubt eine gezielte Steuerung bzw. Einstellung der Materialeigenschaften.
In den bisherigen wissenschaftlichen Arbeiten zu thermoplastischen Nanokompositen
mit sphärischen keramischen Nanofüllstoffen ist die Dispersität der Nanokomposite
nicht hinreichend gut quantifiziert worden, was zur Folge hat, dass verschiedene Herstellungsmethoden
nicht miteinander verglichen werden können. Diese Arbeit zielt darauf
ab, thermoplastische Polyamid 6-Nanoverbundwerkstoffe mit guter Dispersität mittels
Extrusion herzustellen und zu untersuchen. Dabei werden drei Herstellungsmethoden
und die dabei erreichten Dispersionsqualitäten und Eigenschaftsprofile betrachtet. Dafür
werden Verbundwerkstoffe aus einer PA6-Matrix und keramischen Nanofüllstoffen (TiO2,
SiO2, BaSO4) - als Pulver oder als Nanopartikeldispersion - generiert. Die erzeugten
Komposite werden mit TEM-, REM- und -CT-Analysen morphologisch analysiert. Die
Materialeigenschaften werden durch DSC-, DMTA-, GPC-, Viskositätsuntersuchungen
erfasst. Weiterhin werden Kerbschlagbiege- und Zugversuche durchgeführt.
In einem ersten Schritt wird eine häufig angewendete Herstellungsmethode untersucht,
bei der Nanopartikelpulver zum Extrusionsprozess zugegeben werden. Es ist
nicht möglich alle Agglomerate durch die Bearbeitung im Extruder aufzubrechen. Die
Agglomeratfestigkeit für die verwendeten Partikel wird aus den Verläufen der Dispersität
bei mehrfacher Extrusion erfolgreich bestimmt. Die Untersuchung der Vorgänge
bei der Deagglomeration anhand eines Modells zeigt, dass das Verhältnis zwischen
Agglomeratbruch und Erosion von einzelnen Partikeln von der Oberfläche des Agglomerates
für die Materialeigenschaften von maßgeblicher Bedeutung ist. Trotz sehr guter
Dispersionsqualität der TiO2-Komposite und einer guten Partikel-Matrix-Anbindung lassen
sich nur die Festigkeit und Steifigkeit steigern, während die Kerbschlagzähigkeit
vi Kurzfassung
nicht erhöht ist. Die TiO2-Nanopartikel weisen eine relativ geringe Agglomeratfestigkeit
(0,1 MPa) auf, und die Erosion spielt neben Bruch eine wichtige Rolle im Deagglomerationsmechanismus,
weshalb für diese Partikel die Zugabe als Pulver zu empfehlen
ist. Restagglomerate führen jedoch zu Spannungskonzentrationen im Material, was
eine Zähigkeitssteigerung verhindert. SiO2-Nanopartikel dagegen können bei den in
dieser Arbeit gewonnenen Erkenntnissen nicht als Füllstoffe empfohlen werden. Ihre
Agglomerate weisen eine so hohe Festigkeit auf, dass diese überwiegend zerbrechen.
BaSO4 sollte als Pulver nicht verwendet werden, denn es kann mittels Extrusion kaum
dispergiert werden.
In der zweiten Bearbeitungsphase werden die Materialeigenschaften bei der Zugabe
der Nanopartikel als wässrige Dispersion untersucht. Dabei wird die Partikeldispersion
drucklos zugegeben; das Dispersionsmedium kann an der Zugabestelle direkt verdampfen.
Zusammengefasst ist festzustellen, dass Agglomeration an der Zugabestelle zu
verschlechterten mechanischen Eigenschaften führt.
Im dritten Schritt werden wässrige Nanopartikeldispersionen unter Druck in den Extruder
gepumpt, um zu erreichen, dass sich eine Mischung aus flüssiger Dispersion und Polymerschmelze
bildet. Dabei tritt zum einen Diffusion der Partikel in die Polymerschmelze
auf, zum anderen kommt es zu Tropfenverkleinerung durch die Scherspannung im
Extruder. Bei der theoretischen Untersuchung der Zerkleinerung der Dispersionstropfen
wird festgestellt, dass das Verhältnis der Viskositäten der zu mischenden Medien, deren
Oberflächenspannungen und die Scherspannung im Extruder den Vorgang bestimmen.
Die so ermittelte Größe der kleinsten Agglomerate liegt nicht im Nanometerbereich.
Infolge der geringen Mischdauer nach der Verdunstung des Dispergiermediums sind die
Agglomerate schlecht an die Matrix angebunden. Weiterhin bilden sich sehr kompakte
Agglomerate. Aufgrund dessen steigert sich der E-Modul des Nanokomposits kaum
bei einer gleichzeitig reduzierten Zähigkeit. Als Dispersion zugegeben diffundieren die
SiO2-Partikel kaum und es bilden sich relativ große Agglomerate. Da insbesondere bei
TiO2 und BaSO4 außergewöhnlich kleine Agglomerate (<100 nm) bzw. sogar Primärpartikel
gefunden werden, ist davon auszugehen, dass für diese beiden Nanoadditive
auch Diffusion von Bedeutung ist. Nanokomposite mit diesen Füllstoffen sollten über
die Methode der Zugabe von wässrigen Dispersionen unter Druck hergestellt werden.
Diese Arbeit bildet mit systematischen Untersuchungen von industriell relevanten Prozessen
zur Herstellung von Nanokompositen, den Mechanismen, die dabei ablaufen,
und den erzielbaren Materialmorphologien und Materialeigenschaften die Grundlage
für maßgeschneiderte Nanokomposite.
vii
Abstract
Ceramic spherical nanoparticles can significantly increase the properties of thermoplastic
polymers. Well-dispersed nanoparticles can exceptionally increase the material
toughness of polymers. However, agglomeration, which occurs because of an extremely
large specific surface area of the particles, can counteract this behavior. This
is one of the major challenges in nanocomposite science. As industrially produced
nanocomposites are of increasing interest for all kinds of applications, the research of
process-structure-property-relationships of nanocomposites with commercially available
nanoparticles is crucial in engineering science. This allows the control of the material
properties.
Most existing publications about thermoplastic nanocomposites with ceramic spherical
nanofillers do not quantify the dispersity of the products sufficiently. Consequently, the
different production methods cannot be compared. This work studies thermoplastic
polyamide 6 nanocomposites that were produced by extrusion processing in order to
achieve a good dispersion quality. To complete this task, three production methods were
applied and the resulting dispersion quality was analyzed. For this, nanocomposites
consisting of a PA6 matrix and TiO2-, SiO2- and BaSO4-nanofillers - as powders or as
dispersions - were produced. Structural analysis was performed by electron microscopy
and computer tomography. DSC, DMTA, GPC, and viscosity measurements were
executed, and impact and tensile tests conducted.
In a first step, the traditional production method of thermoplastic nanocomposites, where
nanoparticle powders are incorporated in the polymer melt, was analyzed. It was found
that it was impossible to reduce all agglomerates by extrusion. The agglomerate strength
was successfully determined from the dispersion quality when multiple extrusion was
applied. Furthermore, a model revealed the appearing mechanisms of erosion of single
nanoparticles from the agglomerate surface and agglomerate breakage. It was found
that breakage was the dominant mechanism of deagglomeration. Despite very good
dispersion quality of the TiO2-composites and a strong particle matrix interaction, only
material stiffness and strength could be increased, while the impact energy was not
increased. TiO2-nanoparticles are favourable for powdery addition, due to their relatively
small agglomerate strength (0,1 MPa) and the important part that erosion also played in
the deagglomeration mechanisms. Remaining agglomerates behaved as large single
particles and acted as initiation sites for brittle crack behavior. SiO2-nanoparticles are
viii Abstract
not recommended as powdery fillers, because they built very strong agglomerates, that
only exhibit breakage as deagglomeration mechanism. BaSO4 is not recommended as
filler in powder form because of the lack of deagglomeration.
In a second step, the material properties were examined, when the nanocomposites
were produced by unpressurized insertion of aqueous nanoparticle dispersions into the
polymer melt. The dispersion media evaporated immediately after insertion. However,
agglomerates generated during extrusion resulted in reduced mechanical properties.
In a third step, aqueous nanoparticle dispersions were incorporated using enough
pressure to build a blend consisting of dispersion and polymer melt. Two mechanisms
occurred during this process. On the one hand, particles diffused from the dispersing
agent into the polymer melt. On the other hand, bigger drops of the aqueous nanoparticle
dispersion were reduced to smaller ones by shear stresses during extrusion. The
smallest drop size occurring in the latter process could be determined. This size was
affected by the ratio of the viscosity of the media, their surface tensions and the shear
stresses in the extruder. The such calculated smallest agglomerate size was not smaller
than 100 nm in the pursued range. As a result of the short mixing duration after
evaporation of the dispersion fluid, agglomerates were poorly bonded to the matrix.
Furthermore, very dense agglomerates were formed. Thus, the toughness was reduced
while the Young’s modulus could hardly be increased. As dispersions, SiO2-particles
did not undergo a diffusion mechanism ending up in big remaining agglomerates. As
remarkably small nanoparticle agglomerates (<100 nm for TiO2) and primary particles
(BaSO4) could be found, it could be assumed that the diffusion mechanism also occurred.
Thus, the pressurized insertion of nanoparticle dispersions represents an adequate
production method for nanocomposites with BaSO4 and TiO2 as fillers.
This work can be considered as a systematic research on production methods for nanocomposites,
the mechanisms playing a part and the material structures and properties
that are gained. Within the new results and findings of this work it is possible to tailor
nanocomposites.